LOADING DOCK
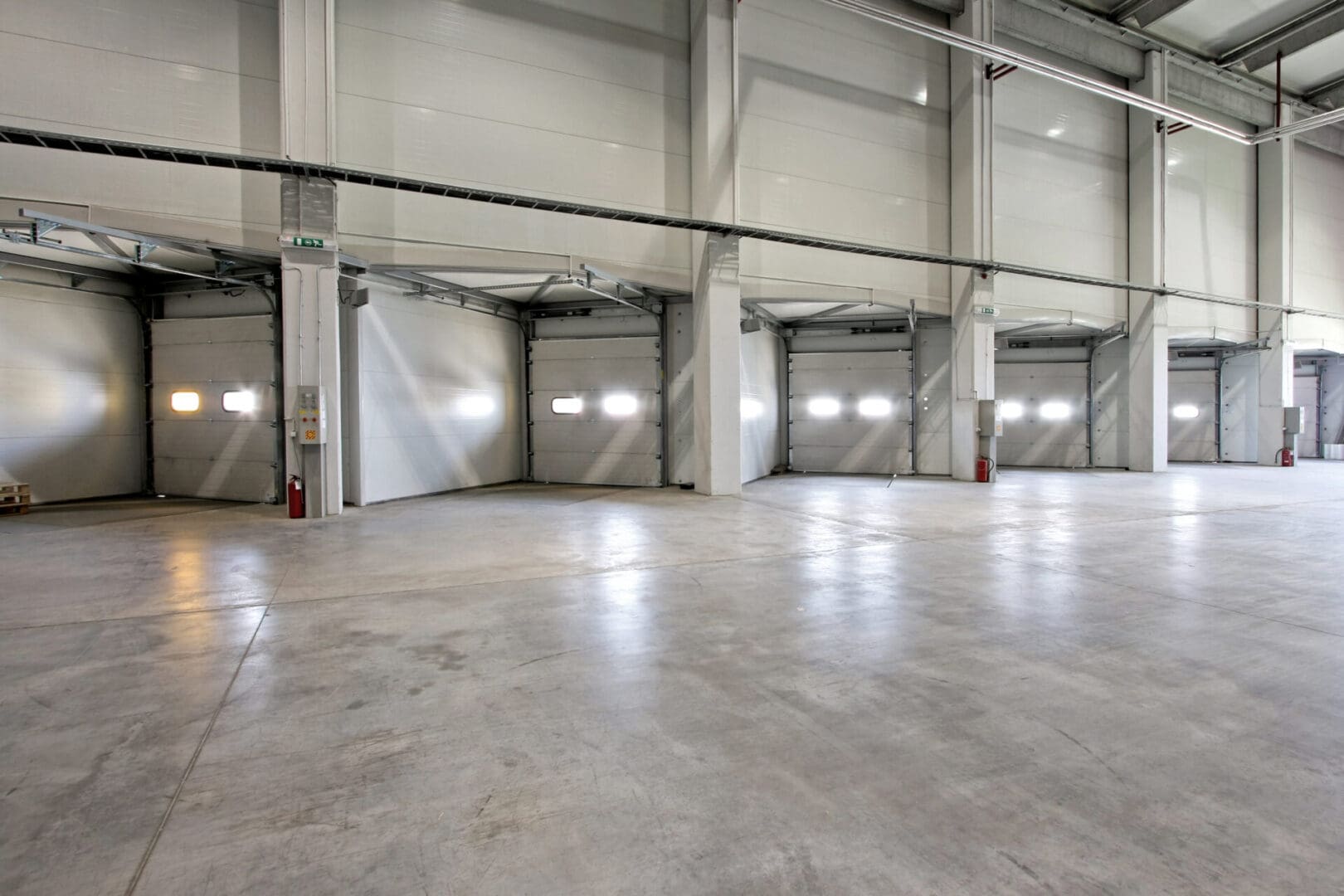
Loading Dock
The major entry points for all items delivered in markets and businesses are loading docks. Practically every product you can buy has travelled through a bustling loading dock at some point. Docks or bays in freight terminals and warehouses, without a doubt, play an important part in business.
With all of the activity in loading docks, it's no surprise that they're a hotbed for injuries and accidents; there are numerous dangers that can arise in a normal port. Slippery floors and poorly built ledges are two of the most common causes of dock accidents, both of which can result in catastrophic falls. Of course, these aren't the only concerns about loading bay safety. Vehicles loading and unloading cargo in the ports might also pose a threat. Collisions can occur, jeopardising not just dock operations but also the items being transported and the workers' safety.
However, developing an effective loading dock system or building a warehouse that follows construction best practises is the first step in reducing injuries and accidents in loading bays. Checking that the docks and storage spaces' floors are strong enough to support the weight of the things and equipment that move through them is one example.
Many of the dangers at the docks can also be avoided by simply employing code-compliant fixtures and materials. Falls and skidding, for example, can be avoided by utilising suitable dock stairs and levellers.
However, having a well-designed facility and investing in materials and fixtures that meet government regulations is just the beginning. The warehouse facility's management and personnel must take a proactive approach to ensure loading dock safety.
Here are some more important safety procedures to take to reduce, if not eliminate, accidents and injuries at the loading docks.
1) Workplace Adoption of New Technology
The technology industry has made great progress in providing tools and software that improve worker safety and streamline business processes. These new technologies can be implemented in facilities that utilise loading docks. Some wearable gadgets and apps, for example, can track worker conditions such as weariness and even heart rate.
Management can change break periods based on the workers' well-being in real time, ensuring that they are not overworked. Workers who are tired are more likely to make mistakes, which can lead to accidents and lower productivity. These apps can also collect data to aid in the analysis of compliance with safety measures by higher-ups.
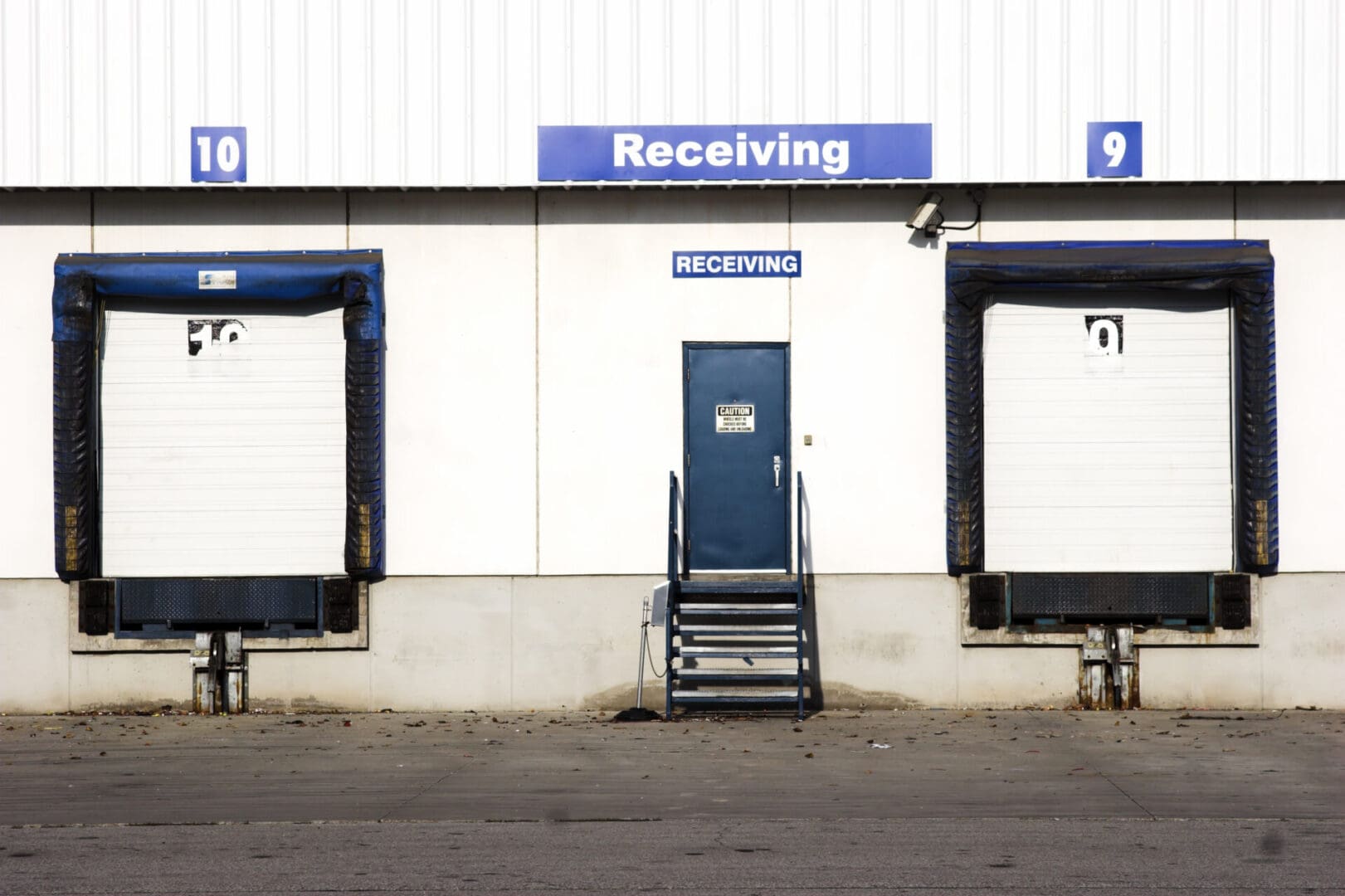
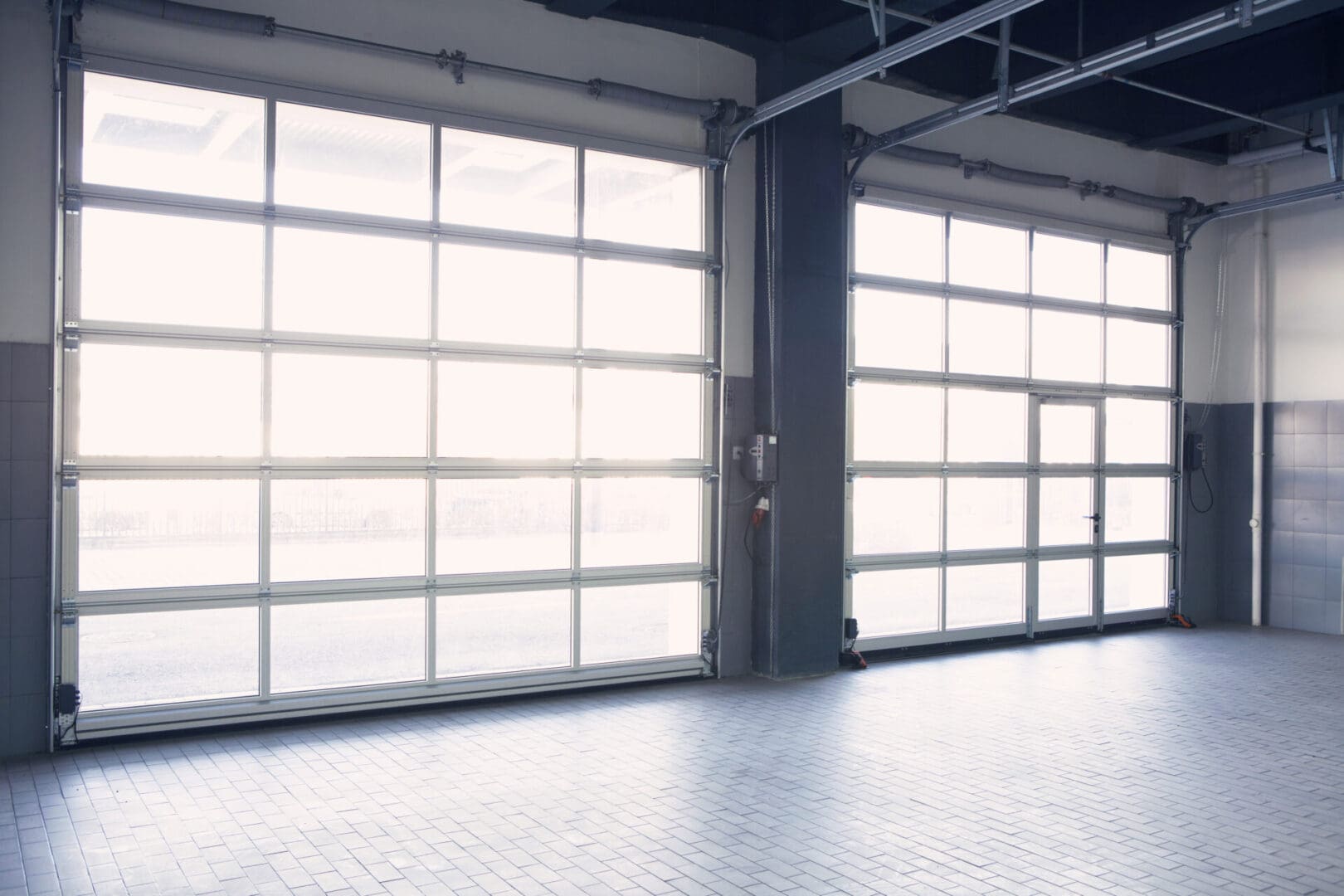
2) Ensure Smooth Vehicular Traffic on-Site
Within the warehouse, the driveways should be designed to provide for smooth traffic flow and simple manoeuvrability for delivery trucks and other vehicles. The same may be said for warehouse interiors, where forklifts are always in operation. Tight spaces can lead to crashes, as well as damage to the building components that house the loading bays, putting workers' safety at risk.
Improved vehicular traffic at warehouses and other businesses that use docks can reduce accidents and provide more elbow room in the event of an emergency.
3) Maintain a Dry Floor
Slipping is a typical occurrence in warehouse loading bays, as previously stated. To avoid this, warehouses may implement procedures that ensure that surfaces remain dry at all times.
Installing doors or barriers to keep rain and snow out of the docks is one option. If the bays are mostly used for wet items, rubber matting can help prevent the flooring from becoming slick.
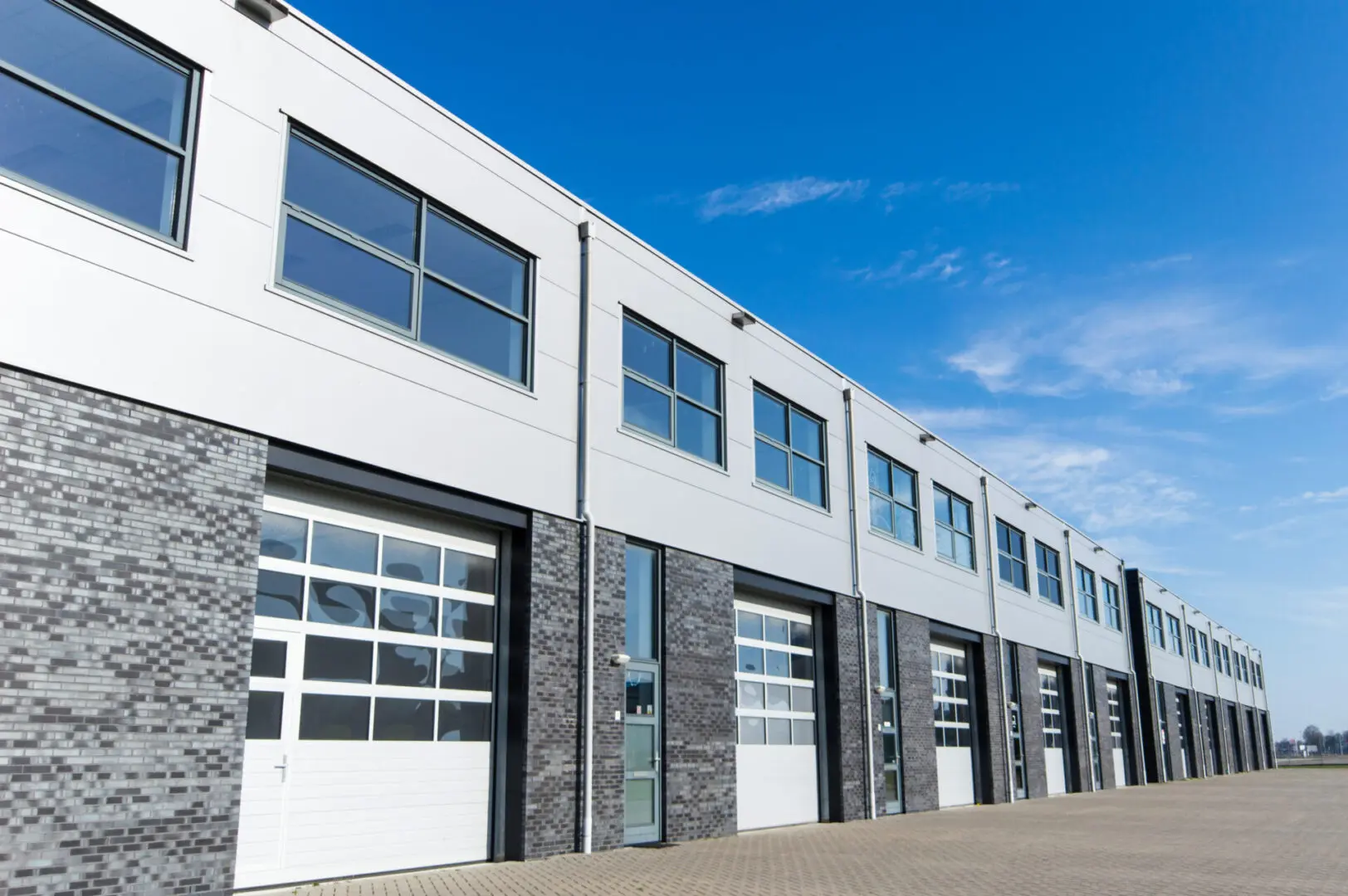
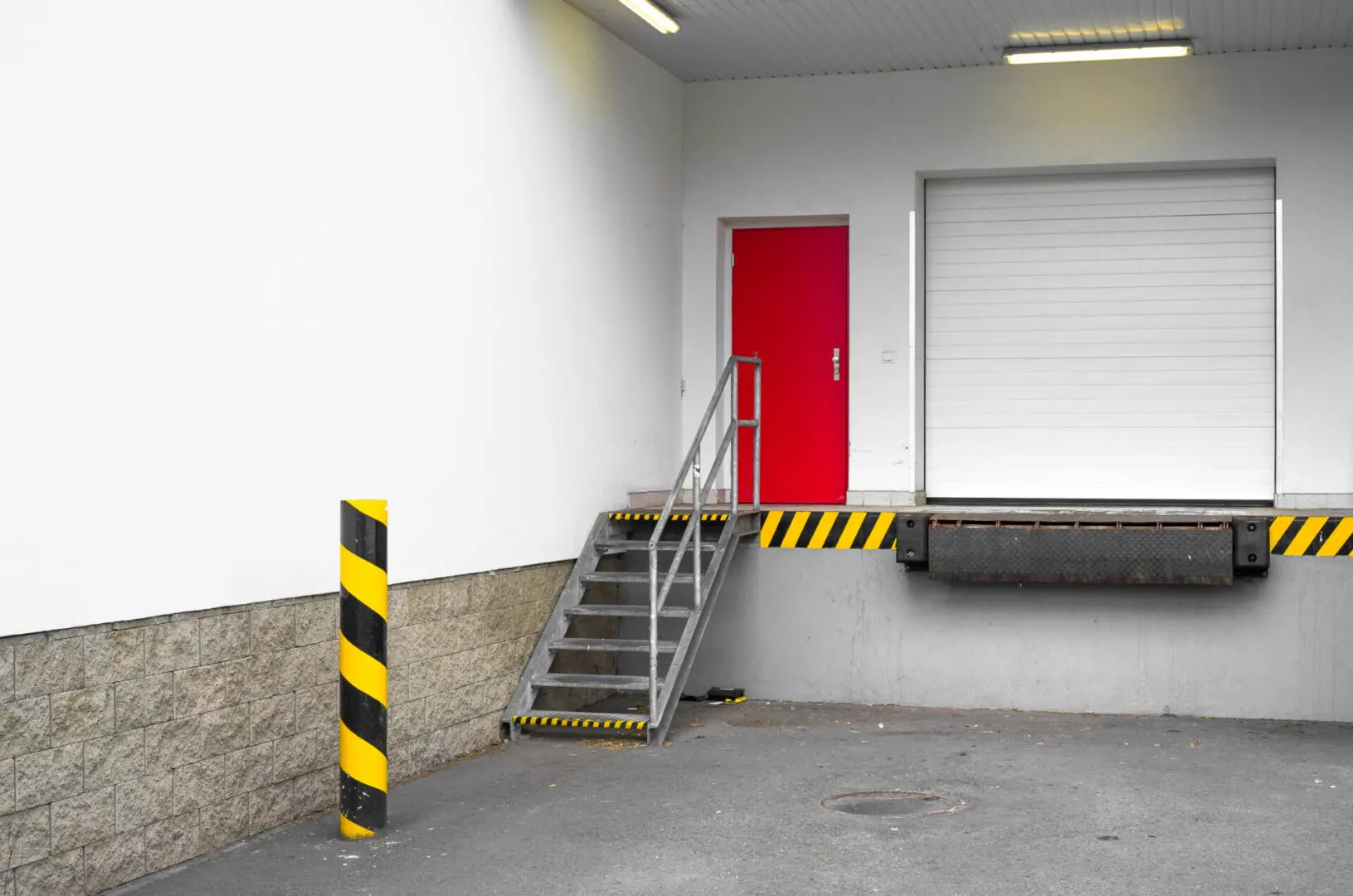
4) Invest in High-Quality Lighting
If dock employees can't see what they're doing, how can they do their duties properly? Lighting in high-traffic locations, such as loading docks, should always be adequate. Aside from increasing productivity, well-lit loading bays can also aid with security and safety. For one thing, workers who can see clearly will be able to recognise hazards and avoid making mistakes.
5) Use the Correct Signage and Warning Signals
Even the most seasoned or well-trained staff are prone to forgetting things. Alerting them to potential dangers is the best approach to keep them on their toes. The hard lifting and stacking that occurs in the ports might cause workers to lose track of where they are. Make sure to paint caution signs on the flooring to let them know how near they are to the dock edges to keep them from falling off the loading bay. Forklift operators should also be aware of where they should park their vehicles.
Outside the warehouse, traffic lights may be helpful in preventing collisions and facilitating the smooth movement of trucks and other vehicles. Speed limits and directional arrows help deter drivers from being careless while also indicating where they should travel inside the facility.
Turning off the motor when loading or unloading the truck can help prevent it from mistakenly rolling away from the dock and leaving a gap between the trailer and the loading bay. When this happens, workers may be at risk of falling. The warehouse safety regulations should also include warnings concerning flammable and dangerous chemicals.
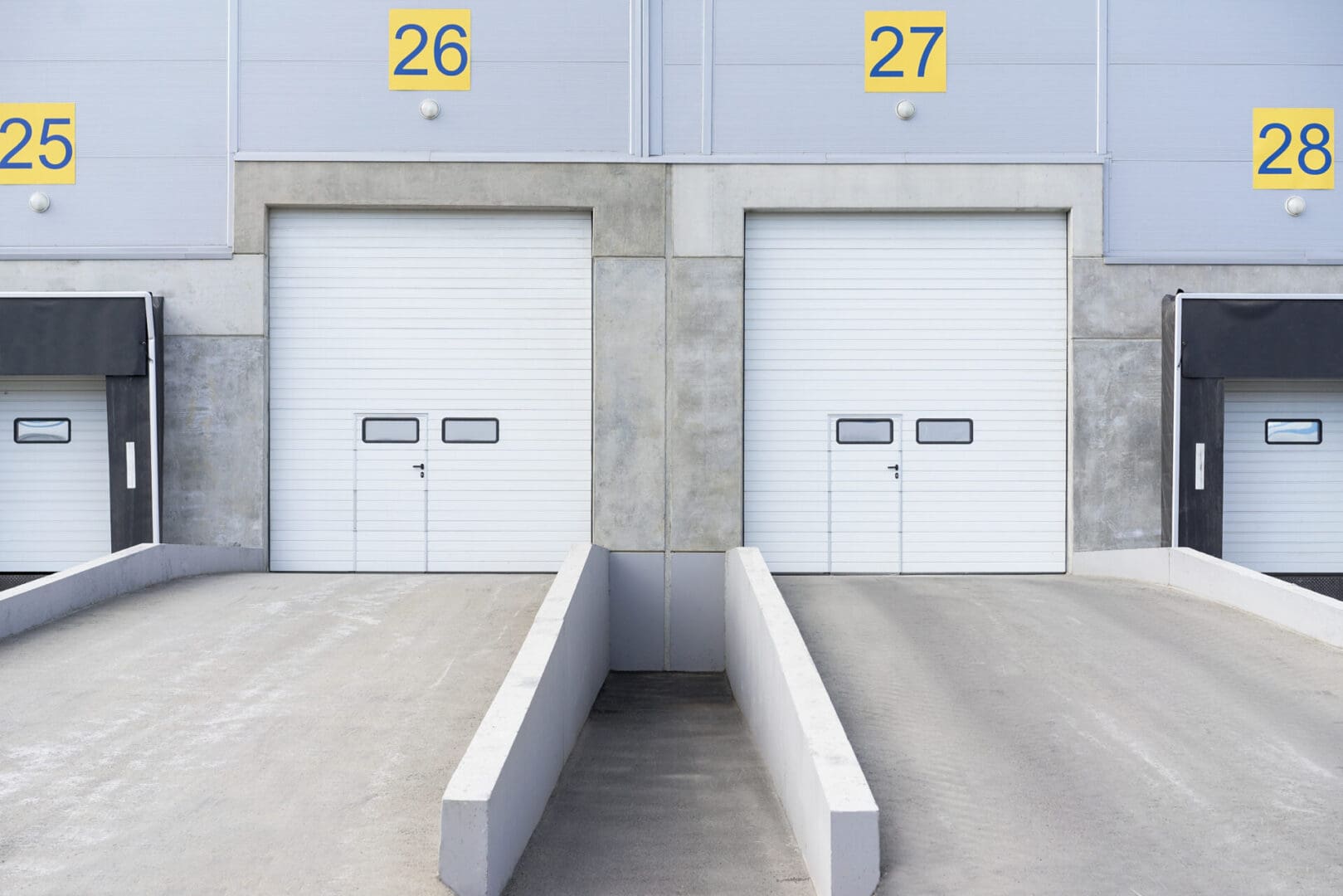
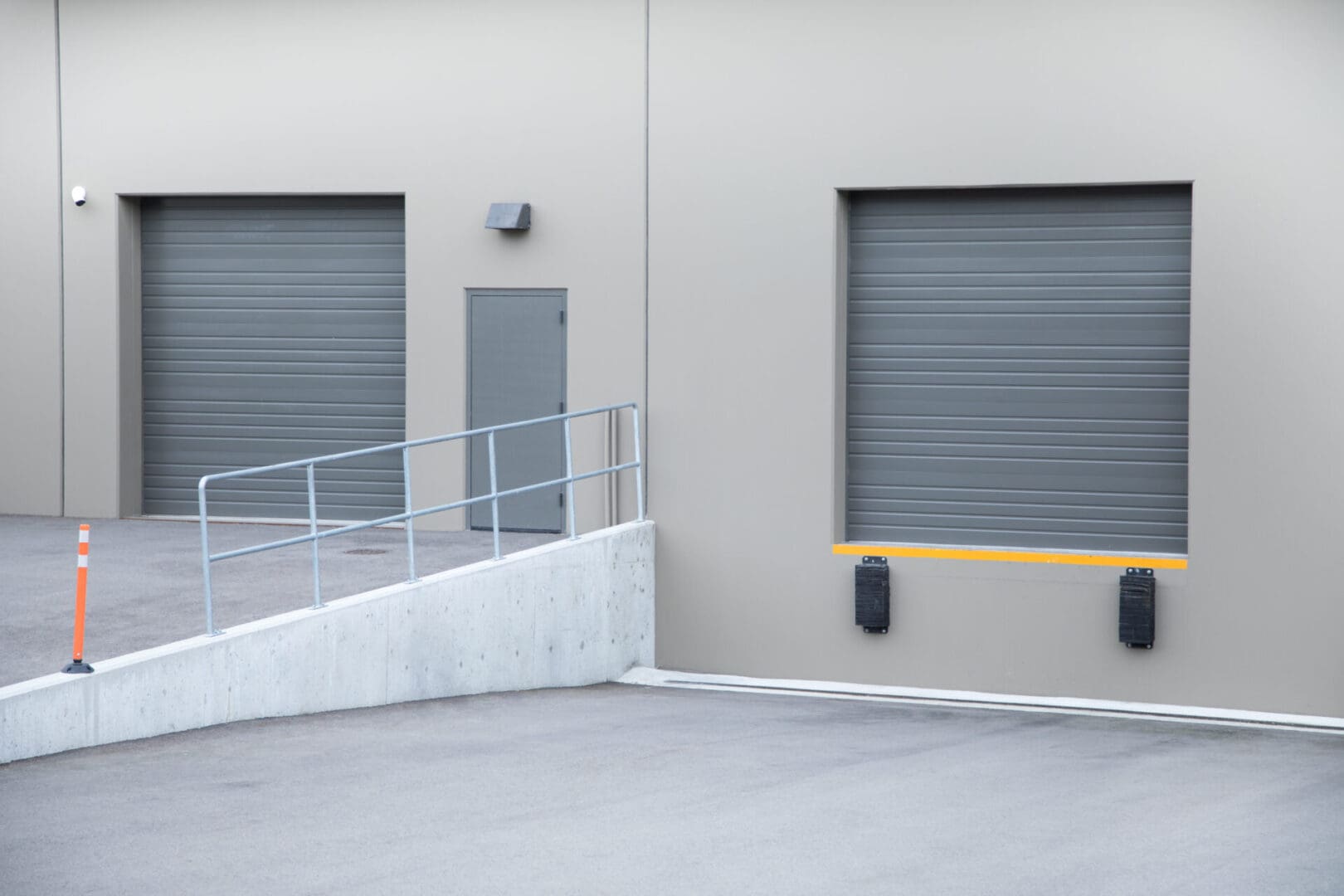
6) Make it Easier for Drivers and Workers to Communicate
Allow truck drivers and dock personnel to communicate efficiently in addition to putting up adequate signage and signalling systems. Two-way radios can be beneficial. Furthermore, it's preferable if you don't leave anything to chance. When the loading or unloading job is over, for example, the individuals involved should know when to remove the clamps that secure the vehicles. When workers and equipment operators agree on which products to stack together or when to take steps in the work process, it helps.
7) Before Using Any Tools or Equipment, Make Sure They are in Good Working Order
Giving all of your tools and equipment a thorough inspection before using them will help you avoid mishaps. Is the battery in the mechanical elevators fully charged? Have the workers double-checked that all power sources are in good working order? Are the dock stairs securely fastened?
It's also a good idea to inspect the docks' cleanliness when you're completing the inspection. A safe working environment is always a positive start in the right direction.
Last Thoughts
Loading docks are high-traffic places. Dock management must assure the safety of all personnel and truck drivers that enter and exit the facility, in addition to having an efficient workflow. Accidents and injuries can result from any blunder or inattention.
Dangers that may arise in the dock area can be avoided with good training and safety practises. Above all, it's critical to follow proper loading dock procedures and invest in the appropriate equipment, which includes anything from dock stairs to durable flooring materials.
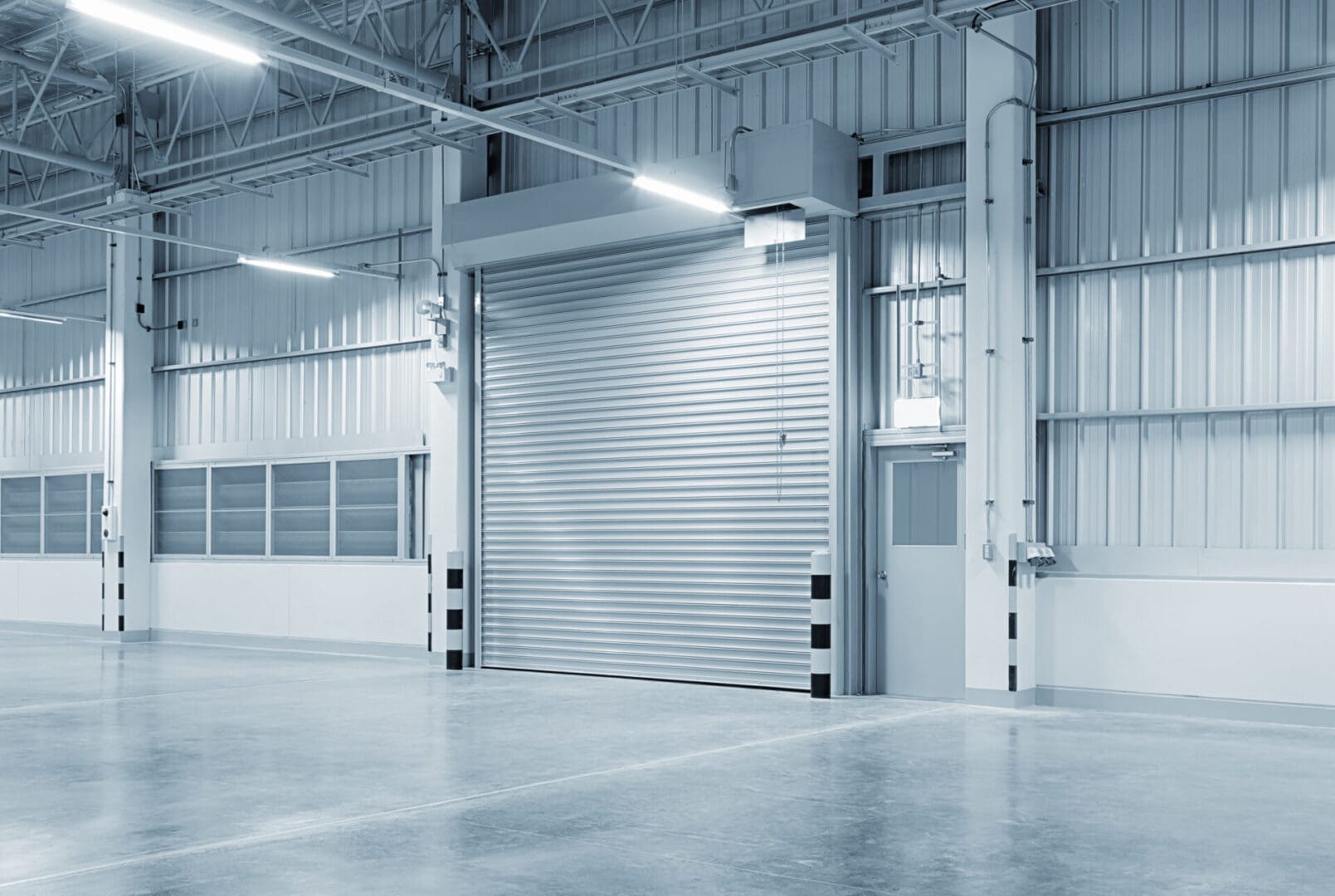